How To Install Copper M Press Profile Fittings
Learn how to install Copper M Press fittings with our step-by-step guide, covering tools, preparation, installation tips, and common mistakes to avoid.
Last Updated: Sep 2, 2024
Press fittings have become increasingly popular in plumbing and heating systems due to their quick, reliable, and flame-free installation process. Unlike traditional soldering or brazing methods, Press fittings use mechanical force to create a watertight seal, making them ideal for both residential and commercial applications.
There are various types of Press Fittings, but this guide will take you through everything you need to know about installing Copper M Press Profile fittings, including the tools required, step-by-step installation instructions, best practices, and common mistakes to avoid.
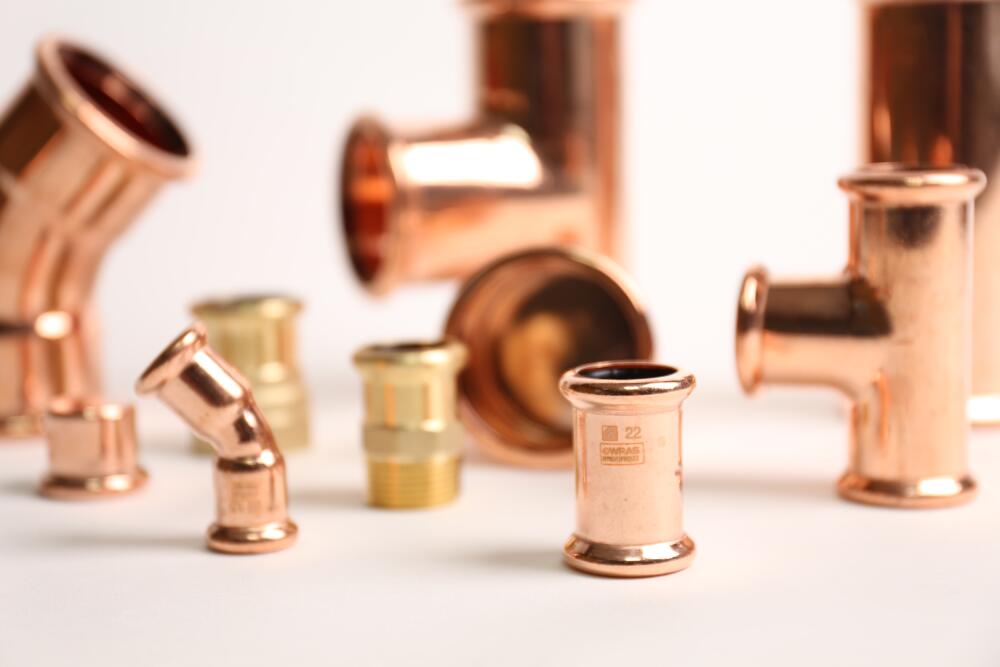
Copper Press
Explore Flowflex Copper Press fittings, perfect for various applications including domestic, commercial, and industrial. These heat-free, visually appealing joints ensure quick, efficient installations. With WRAS approval and sizes ranging from 15mm to 108mm, they offer a dependable and economical solution. Click to see our full range of M-Profile Copper Press fittings.
What Are Copper M Press Fittings?
Copper M Press fittings are mechanical fittings designed to connect copper pipes without the need for heat or solder. These fittings use an innovative press tool to compress a sealing element, usually made of EPDM (ethylene propylene diene monomer), between the pipe and the fitting, creating a strong and durable seal.
The key components of a Copper M Press fitting connection include:
The Fitting Body: Made from copper, the body is designed to fit around the pipe and is often marked with indicators showing where to place the press tool.
The Sealing Ring: Typically made from EPDM, the sealing ring is compressed during installation to form a watertight seal.
The Copper Pipe: Manufactured to BS EN 1057 standards.
Advantages of Copper M Press Profile Fittings
Fast and Easy Installation
The installation of Press Fittings is very quick, saving time compared to other methods like soldering, brazing or using Compression Fittings.Minimal Training Required
Unlike more traditional methods, Press Fittings are easy to learn and use.No Flame Required
Since no heat is used, Press fittings are ideal for installations in areas where flames are restricted or pose a fire risk.Reliable and Leak-Proof
When installed correctly, Press fittings provide a secure, leak-proof connection that meets industry standards.Can Be Installed When Wet
No need to drain water out of the system during installationEnvironmentally Friendly
Copper, Brass and Steel are all highly recyclable materials, making metal Press Fittings an environmentally friendly option for your project.Neat, Aesthetic Appearance
Press fittings offer a sleek, professional look that is great when aesthetics are important. Their streamlined design blends seamlessly with the pipework, making them suitable for visible applications in both residential and commercial settings.Versatile Applications
Press Fittings are suitable for hot and cold water, heating systems, compressed air, and some gas applications (depending on the type of o-ring used).Reduced Risk of Installation Errors
The precision of the press tool minimises the risk of errors during installation. The tool’s built-in safety features, such as press indicators, ensure that each fitting is correctly compressed, resulting in a secure and leak-proof connection.
Installing Copper M Press Fittings
Preparing Your Copper Tube
Proper preparation of the pipes and fittings is essential for a successful installation. Follow these steps to prepare your materials:
Equipment
Tools
- Pipe Cutter
- Deburring Tool
- Hand Protection
Supplies
- Copper Pipe
Installation Steps
Cut Your Pipe To Size
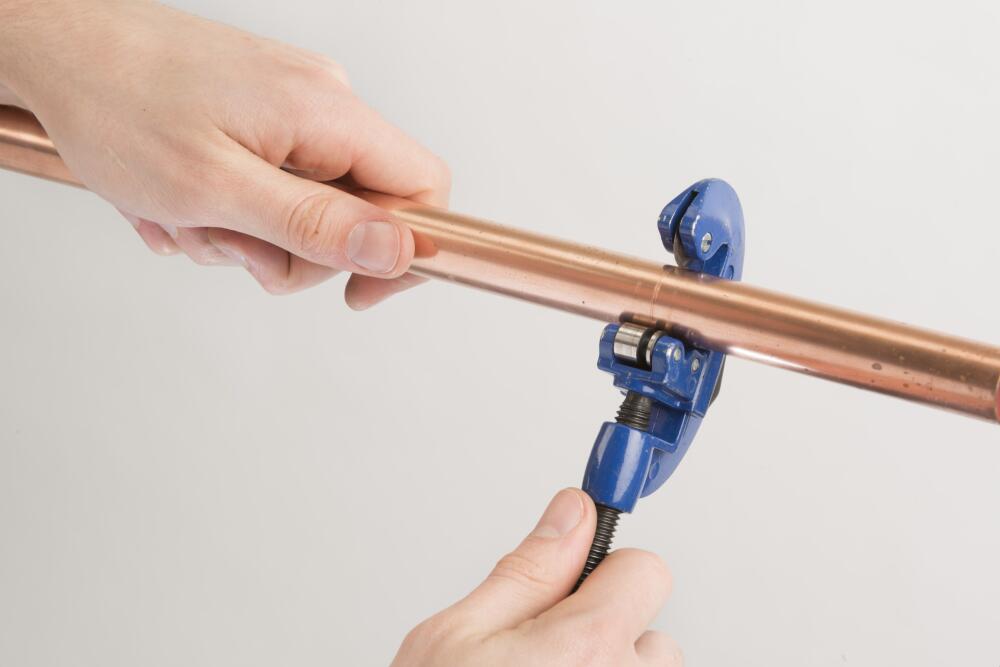
Cut your pipe cleanly across the tube diameter using a good quality pipe cutter or rotary pipe cutter.
Cut Your Pipe Accurately
It is important to ensure that the pipe ends are clean and cut square. Failure to do so could impact on the quality of your jointing. If your cut is not flat, or your pipe is too short, the pipe may not hit the pipe stop compromising the joint integrity. Too long and you may introduce strain into the whole system.
Clean The Socket Of The Pipe
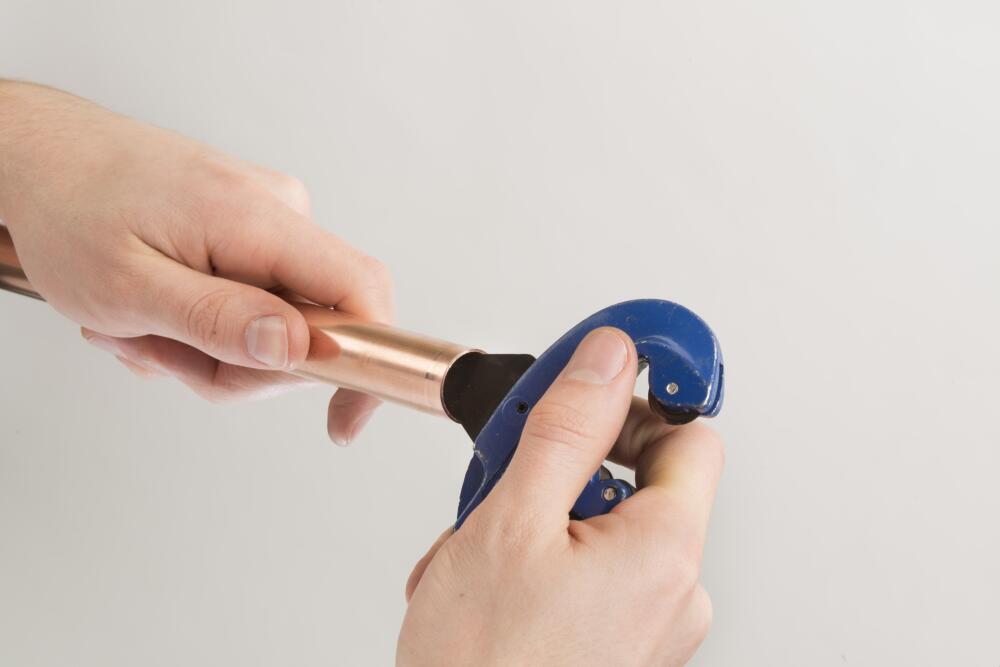
Using your deburring tool, make sure the inside of the pipe is smooth and will not interfere with the flow.
Clean The Outside Of The Pipe
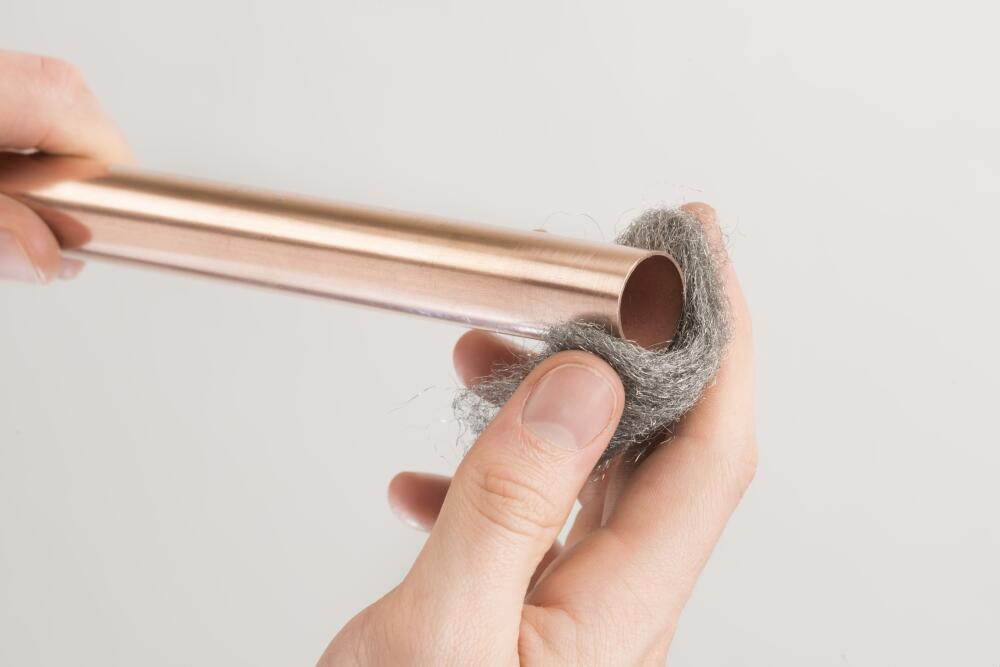
Clean the outside of the pipe, making sure that there is no pipe residue, dirt or grit is present near the joint. Failure to remove all oxides and any material where the fittings and tube overlap can interfere with the capillary action and thus will reduce the strength of the soldered joint, resulting in failure.
To the same effect, over zealous cleaning can result in too much material being removed, resulting in a loose fit and failure.
Connecting The Copper M Press Fittings
Once your pipes and fittings are prepared, follow these steps to complete the installation:
Equipment
Tools
- Press Tooling - 'M' Profile Jaws
- Press Gun
Supplies
- Pipe
- M Profile Press Fittings
Installation Steps
Check And Mark
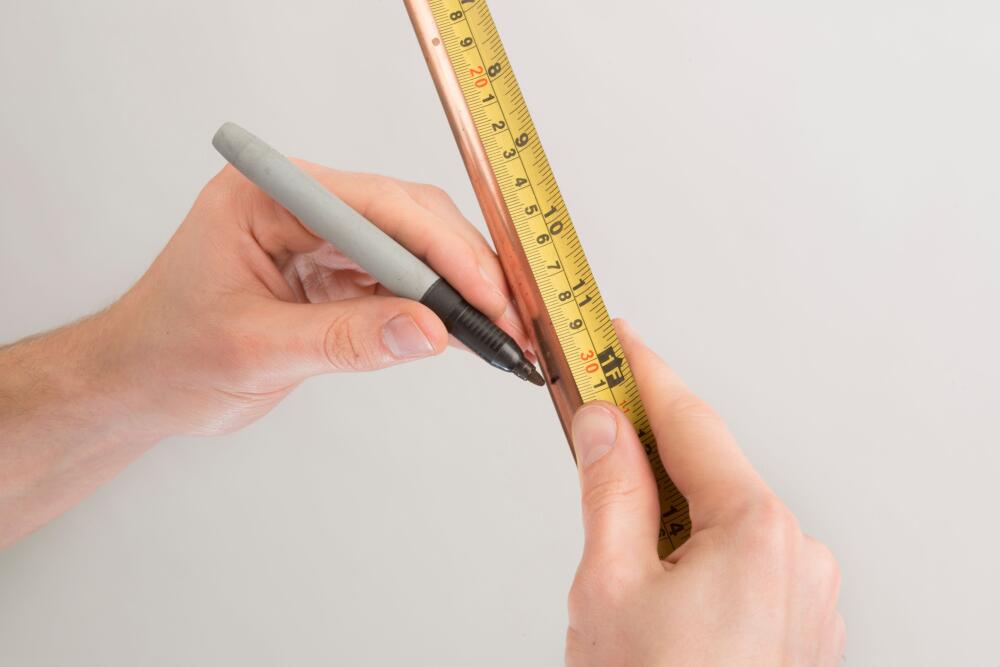
Before inserting the pipe, check the O-ring is present, lubricated and free from damage.
Insert the tube into the fitting up until it hits the pipe stop. Mark the insertion depth with a black marker on the tube to ensure the pipe has been fully inserted before pressing.
Make Sure Everything Is Clean and Free of Debris
It is important that the outside of the pipe and the socket of the fitting are clean and free from debris. Any debris could damage the O-Ring on insertion.
Crimp The Fitting
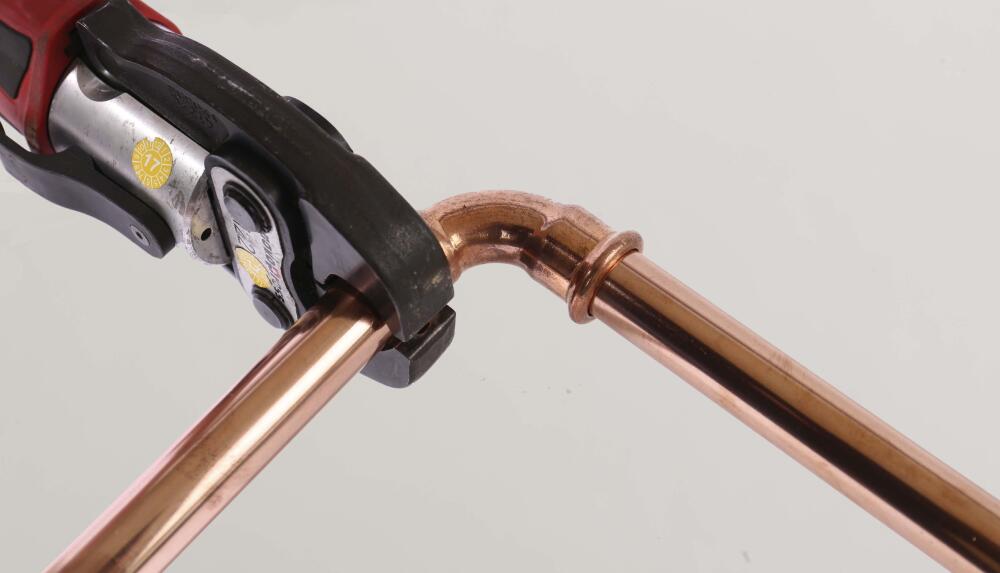
Ensure you select the correct size jaw and that the jaw is M profile. The jaw must be placed square on the fitting and the joint is only complete when the mouth of the fitting is fully enclosed by the jaws.
After the press cycle is complete remove the jaws and check that the socket depth marking on the pipe has remained in place, adjacent to the now pressed mouth of the fitting.
Best Practices and Tips
Ensure Proper Alignment
Misalignment of the pipe and fitting during pressing can lead to an incomplete seal. Always ensure the pipe is fully inserted and aligned correctly before pressing.Use the Right Press Jaws
Each fitting size requires a specific press jaw. Using the incorrect size can lead to poor seals or damaged fittings.Keep Your Fittings Clean
Dirt and debris can compromise the seal. Always clean the pipe and fitting thoroughly before assembly.Mark Your Fitting After Pressing
Having a quick visual reference to show that you have pressed each fitting can be really useful when you come to commission your system.Regularly Maintain Your Press Tool
Proper maintenance of your press tool, including calibration and jaw inspection, is essential for ensuring reliable connections.
Common Mistakes to Avoid
Incomplete Pressing
Failing to fully compress the fitting can result in leaks. Always ensure the press tool completes its cycle before releasing the jaws.Damaging the Sealing Ring
Burrs, sharp edges, or improper handling can damage the sealing ring, compromising the seal. Always deburr and inspect the pipe ends.Using Incorrect Tools
M Press fittings require specific tools for proper installation. Using the wrong tools can damage fittings and lead to poor connections.
Wrapping Up
Copper M Press fittings offer a fast, reliable, and flame-free solution for connecting copper pipes in plumbing and heating systems. By following the proper preparation and installation steps, using the correct tools, and adhering to best practices, you can achieve secure and leak-proof connections every time.
Related Articles
Any Questions?
Our team is available for you anytime.