Understanding Gate Valves: Types, Applications, and Benefits
Gate valves are isolation valves ideal for high-pressure, high-temperature uses. Types include Parallel, Wedge, and Rising stems. Learn more here.
Last Updated: Sep 8, 2024
Gate valves are one of the most widely used valves globally, serving crucial roles in various industries, including oil and gas, pharmaceuticals, manufacturing, automotive, and marine sectors. They are used both above and below ground to control the flow of liquids and gases.
Gate valves function as isolation valves, allowing or stopping flow when manually operated by turning the valve handle. They are designed to be either fully open or fully closed, and should not be used for flow regulation or control.
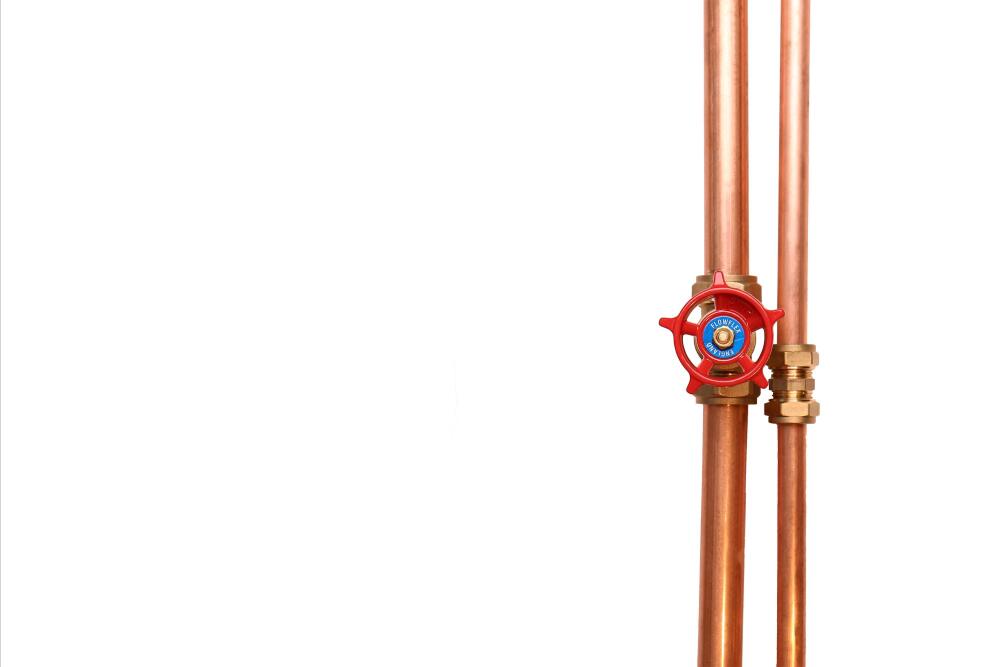
Gate Valves
How Does a Gate Valve Work?
The construction, operation, and performance conditions of Gate Valves is heavily defined by the BS EN 12288 standard. This standard ensures their reliability, safety, performance, and compatibility with other components within the system.
Read Now
Understanding BS EN 12288: Ensuring High Quality Gate Valves and Safety
Key Components of a Gate Valve
A gate valve consists of several key components, each playing a crucial role in its operation. Here’s a list of the most important parts:
Body: Main outer shell housing all internal parts; connects to the piping system.
Gate (Disc): Moves up and down to control flow; blocks flow when down.
Stem: Shaft connecting the gate to the handwheel or actuator, moving the gate.
Handwheel/Actuator: Manual or automated control to move the stem and gate.
Seat: Sealing surface where the gate contacts the valve body when closed.
Valve Ports (Inlet and Outlet): Openings for fluid entry and exit.
The Operating Mechanism of a Gate Valve
The components listed above work together to control the flow of fluid through the valve. When you the handwheel or actuator is turned, it moves the stem, which lifts or lowers the gate inside the valve. If the gate is raised, the fluid can flow through easily. If the gate is lowered, it presses against the seat, blocking the flow completely.
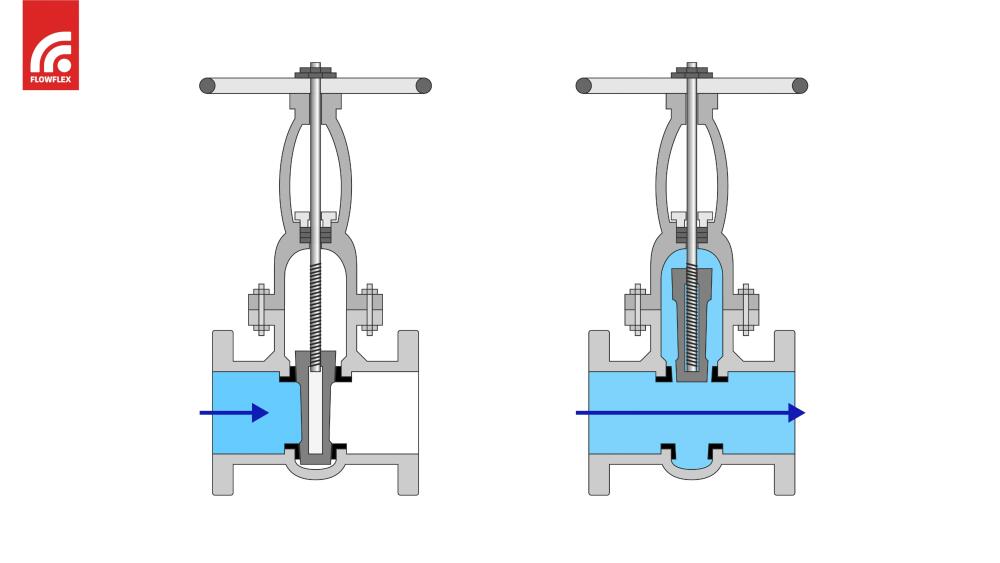
This straightforward design makes gate valves great for fully opening or closing the flow in a system, making them perfect for handling water, oil, gas, and other fluids with little resistance when open and a tight seal when closed.
Common Applications of Gate valves
Gate valves are versatile components used across a wide range of plumbing and industrial applications, including the oil and gas sector, landscaping and irrigation, pharmaceuticals, manufacturing and marine industries. Suitable for both above-ground and underground installations, Gate Valves are strong and resilient, built to perform in demanding environments such as high-pressure and high-temperature settings. As such they are one of the most commonly used valve types.
Gate valves are particularly advantageous in applications involving slurries, as the disc (or wedge) can effectively cut through dense or viscous fluids. They are designed to minimise pressure drop when fully open and provide a complete shut-off when closed, making them ideal as isolation valves in pipelines.
Overall, Gate Valves are intended for full open or full closed service and are not suitable for flow control or regulation.
What Types Of Gate Valve Are There?
Gate valves come in various designs, each suited to specific applications. The main types include Parallel and Wedge-Shaped Gates, Metal and Resilient Seated valves, and Rising and Non-Rising Stem valves.
Parallel and Wedge-Shaped Gates
These designs differ in the disc mechanism inside the valve. Parallel Gate Valves feature a flat disc positioned between two parallel seats, while Wedge-Shaped Gate Valves use an inclined, wedge-like disc to form a tighter seal.
Metal Seated and Resilient Seated
Metal Seated Gate Valves have a grooved base where the disc sits when fully closed, providing a durable seal. Resilient Seated Gate Valves, on the other hand, have a smooth bottom that allows free passage of fluids and suspended particles, making them ideal for applications where debris might be present.
Rising and Non-Rising Stems
Rising Stem Gate Valves have a stem that moves with the disc, providing a visual indicator of the valve’s position. Non-Rising Stem Gate Valves have a stem that remains stationary, making them more compact and suitable for applications where space is limited.
Series A vs Series B Gate Valves
Series A Valves
Designed for flanged and threaded end connections.
Suitable for higher pressure/temperature ratings, aligning with those specified in the flange standards, EN 1092-3.
Series B Valves
Designed for flanged, threaded, capillary, compression, and loose nut/union end connections.
Have lower allowable pressures at elevated temperatures compared to Series A valves, making them suitable for applications with less demanding pressure/temperature requirements.
Common Materials for Gate valve
Gate valves are constructed from a variety of materials, each chosen based on the specific requirements of the application. The selection of material plays a crucial role in ensuring the valve’s performance, durability, and compatibility with the fluid being controlled and other components in the system. Below are some of the most common materials used for manufacturing gate valves:
Cast Iron: Cast iron gate valves are widely used in large-scale industrial applications and municipal water systems due to their durability, cost-effectiveness, and ability to withstand high pressures.
Ductile Iron: Similar to cast iron, ductile iron is stronger and more flexible, making it suitable for high-demand applications where cast iron might fail under stress. This does however, generally, make it more expensive.
Stainless Steel: Highly resistant to corrosion and temperature extremes, stainless steel gate valves are commonly used in chemical, pharmaceutical, and food processing industries. They are ideal for applications involving corrosive or abrasive fluids or where there is a requirement for a high degree of cleanliness.
Bronze Gate Valves: Bronze gate valves offer high levels of corrosion resistance, particularly in seawater and other marine applications. They are commonly used in the marine and oil industries due to their durability and ability to withstand harsh environmental conditions.
Brass Gate Valves: Often used in plumbing, irrigation and industrial applications, brass gate valves provide good corrosion resistance and are easy to manufacture. They are a popular choice due to their relatively low cost.
Choosing the right material for a gate valve is essential for ensuring reliable performance, longevity, and safety in your specific application. Always consider the operating conditions, including pressure, temperature, and the nature of the fluid or gas being transported, when selecting the valve material.
Read Now
Selecting the Right Material for Your Gate Valve
Why Choose A Gate Valve
Gate valves are a preferred choice across many industries due to their reliable performance and versatile applications. They offer several distinct advantages, such as simple operation, excellent sealing capabilities, and suitability for high-pressure environments, making them ideal for systems requiring full on/off control. However, like any component, they have specific limitations that need consideration.
Below, we dive into the key advantages and potential drawbacks of gate valves to help you determine if they are the right fit for your needs:
Advantages of a Gate Valve
Simple and Reliable Operation
Gate valves have a straightforward design with fewer moving parts compared to other valve types, making them easy to operate and maintain. This simplicity contributes to their reliability and long service life.Bi-Directional Flow
Gate valves can be installed in either direction, allowing fluid to flow from both sides. This flexibility is useful in applications where flow direction may change or needs to be controlled from multiple directions.Excellent Sealing Capability
Gate valves provide a tight seal when fully closed, which makes them ideal for isolation purposes. The gate presses firmly against the seat, effectively blocking the flow of fluid and preventing leakage.Effective In High-Pressure and High-Temperature Applications
Gate valves are designed to handle a wide range of pressures and temperatures, making them suitable for demanding industrial environments such as oil and gas pipelines, power plants, and chemical processing.Versatility in Applications
Gate valves are used across various industries, including water supply, wastewater treatment, irrigation, oil and gas, power generation, and chemical processing, due to their versatility in handling different types of fluids, including liquids, gases, and slurries.Reduces the risk of Water Hammer
The threaded operation of a Gate Valve allows for gradual opening and closing, which reduces the risk of water hammer and prevents damage to the system.Read Now
Hydraulic Shock: Causes, Impacts, and How to Prevent Water Hammer
Limitations of a Gate Valve
Not Suitable for Regulating Flow
Gate valves are not designed for throttling or regulating flow. Partially opening a gate valve can cause vibration, noise, and uneven wear on the gate and seat, leading to premature failure. Throttling can also result in cavitation, damaging the valve.Slow Operation
Gate valves can be slow to open and close compared to other types, such as ball valves or butterfly valves. This slower operation time makes them less suitable for applications requiring quick shutoff or emergency control.
Gate Valve Size Classification
Choosing the correct size of gate valve is crucial for ensuring compatibility with your piping and system requirements. The table below provides a detailed overview of common gate valve sizes and their corresponding dimensions for various end types, such as threaded ends, capillary ends, and compression ends for both copper and plastic tubes. This guide will assist you in selecting the appropriate valve size for your specific application, ensuring a precise fit and optimal performance of your system.
Nominal Valve Sizes | ||||
---|---|---|---|---|
DN | Threaded Ends | Capillary ends | Compression ends for | |
Copper Tube | Plastic Tube | |||
DN 10 | 3/8 | 10 | 10 | 12 |
DN 15 | 1/2 | 15 | 15 | 16 |
DN 20 | 3/4 | 22 | 22 | 20 |
DN 25 | 1 | 28 | 28 | 25 |
DN 32 | 1 1/4 | 35 | 35 | 32 |
DN 40 | 1 1/2 | 42 | 42 | 40 |
DN 50 | 2 | 54 | 54 | 50 |
DN 65 | 2 1/2 | 66.7, 76.1 | 66.7, 76.1 | 63 |
DN 80 | 3 | 88.9 | 88.9 | 75 |
DN 100 | 4 | 108 | 108 | 110 |
Key Factors to Consider When Selecting a Gate Valve
When selecting the right Gate Valve, consider the following factors:
Material Compatibility: Ensure the material of the ball valve is suited for environment in which it will perform.
Pressure and Temperature Ratings: Check that the valve can handle the design system pressures and temperatures.
End Connections: Choose the correct connection type (e.g., flanged, threaded, capillary, or compression) based on required working conditions, the safety considerations for your site and the skill level of your labour to ensure a secure and leak-free installation.
Operation Mechanism: Choose between manual or automated (actuated) operation depending on your design requirements, particularly for industrial or hard-to-reach installations. For space-constrained areas, a non-rising stem gate valve is an ideal option.
Handwheel or Lockshield: Need to restrict access to your Gate Valve for authorised personnel only? In that case, consider using a lockshield Gate Valve for added security.
Compliance with Standards: Verify that your Gate Valves are compliant with the standards to ensure safety and high-quality performance in your applications.
Performance of Flowflex Gate Valves
Flowflex Gate Valves are known for their reliable and efficient performance in various applications. Below, we highlight key performance data that demonstrate their durability and suitability for different pressures and temperatures:
All working conditions assume that the components have been assembled and connected correctly, and adhere to their respective tube compatibility.
If you are planning to use our products in applications outside the scope of our recommendations, approval must be sought from us beforehand. Please contact us in these cases.
Compression Gate Valves
Temperature (°C) | Pressure (Bar) |
---|---|
P474 & P474LS | |
-20 | 16 |
120 | 16 |
120 | 0 |
L197 | |
0 | 16 |
99 | 16 |
99 | 0 |
Female Gate Valves
Temperature (°C) | Pressure (Bar) |
---|---|
L198 & L198LS | |
-10 | 20 |
100 | 20 |
100 | 9 |
180 | 9 |
180 | 0 |
L196 | |
-10 | 20 |
100 | 20 |
100 | 9 |
120 | 9 |
120 | 0 |
The performance of Flowflex Valves depends on proper installation and regular maintenance. For tips on how to care for your Flowflex Valves, explore our guidance here:
Read Now
Installation and Maintenance Tips for Flowflex Valves
Wrapping Up
Gate valves are among the most widely used valves globally, thanks to their versatility, reliability, and ability to handle various fluids under high-pressure and high-temperature conditions. Their simple design, bi-directional flow capability, and excellent sealing properties make them indispensable in many industries such as oil and gas, manufacturing, automotive and marine. However, gate valves are designed for on/off applications rather than flow regulation.
Flowflex manufactures a range of high-quality gate valves that meet stringent standards, providing reliable and efficient solutions across various applications. By choosing the right gate valve, you can enhance the performance and safety of your piping systems, ensuring a smooth and uninterrupted operation.
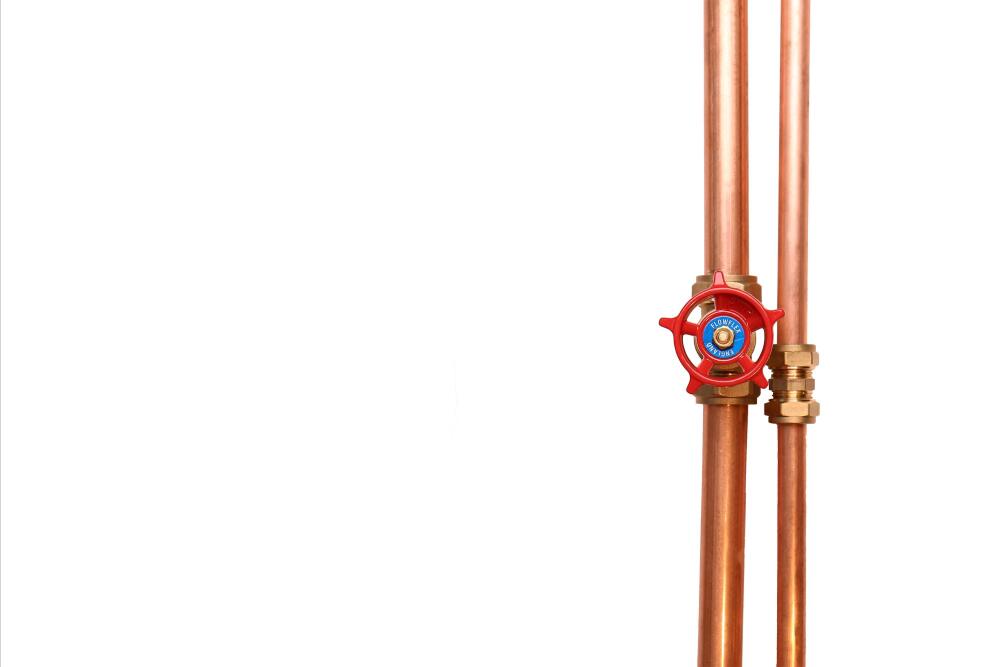
Gate Valves
Related Articles
-
-
Sep 9, 2024
-
-
-
Any Questions?
Our team is available for you anytime.