The Complete Guide to Ball Valves: Features, Applications, and Selection Tips
Explore ball valves, their applications, types, and key factors to choose the right one for plumbing, HVAC, and industrial systems.
Last Updated: Sep 8, 2024
Ball Valves are a crucial component in plumbing, HVAC, and industrial systems, offering reliable control over the flow of liquids and gases. Known for their versatility, ease of operation, and minimal maintenance, Ball Valves are a preferred choice in many applications.
In this guide, we will explore the features of ball valves, their applications, and key factors to consider when selecting the right valve for your needs, with a particular focus on copper alloy ball valves made to BS EN 13547 standards.
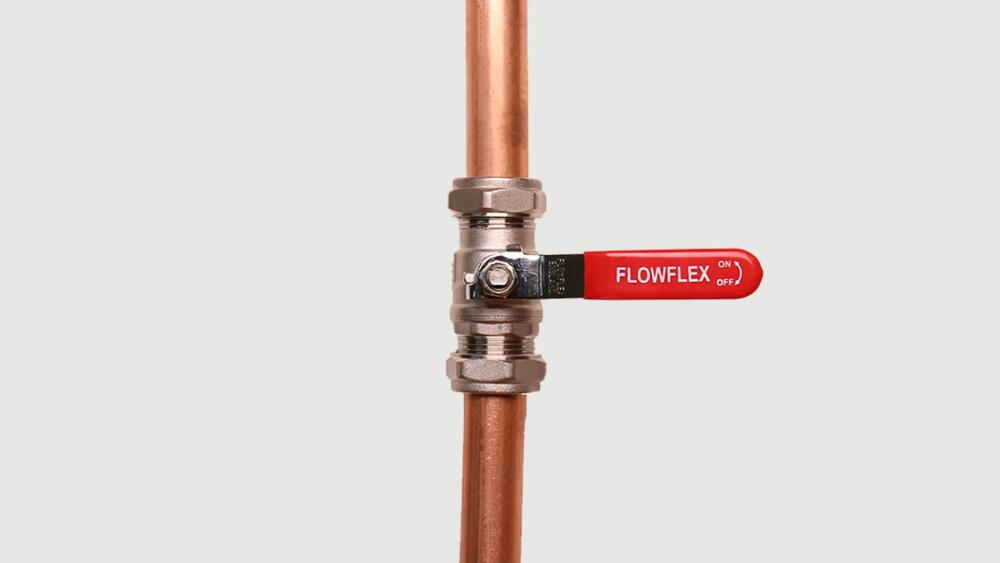
Ball Valves
How Does a Ball Valve Work?
The way Ball Valves are constructed, the way they operate and the conditions under which they can perform is heavily governed by the BS EN 13547 standard, to ensure reliability, performance, safety and compatibility with other products in the system.
Key Components of a Ball Valve
A Ball Valve consists of several key components, each playing a crucial role in its operation. Here’s a list of the most important parts:
Body: Main outer shell housing all internal parts; connects to the piping system.
Stem: Shaft connecting the ball to the lever or other operating mechanism.
Hollow Ball: Controlled and revolves with the stem inside the valve.
Seat: Sealing surface on which the ball sits.
Valve Ports (Inlet and Outlet): Openings for fluid entry and exit.
The Mechanism of a Ball Valve
A ball valve works by interrupting or permitting the flow of liquid or gas. The ball has a hole through the middle, and when the valve handle is turned, the hole aligns with the flow path, allowing the liquid or gas to pass through. When returned through 90 degrees, the ball blocks the flow.

Common Applications of Ball valves
Ball valves are used in a wide range of applications due to their reliable sealing, ease of use, and ability to handle high pressures and temperatures. Some common applications include:
Plumbing Systems: Ball valves are often used as shut-off valves in water supply lines, ensuring a secure and leak-free flow of water.
HVAC Systems: In heating and cooling systems, ball valves control the flow of refrigerants and other fluids, enhancing system efficiency and safety.
Gas and Fuel Lines: Ball valves provide tight shut-off capabilities, making them ideal for gas distribution systems where preventing leaks is critical.
Industrial Processes: In chemical, oil, and gas industries, ball valves control the flow of corrosive or hazardous fluids, offering durability and reliable performance under demanding conditions.
Types of Ball Valves
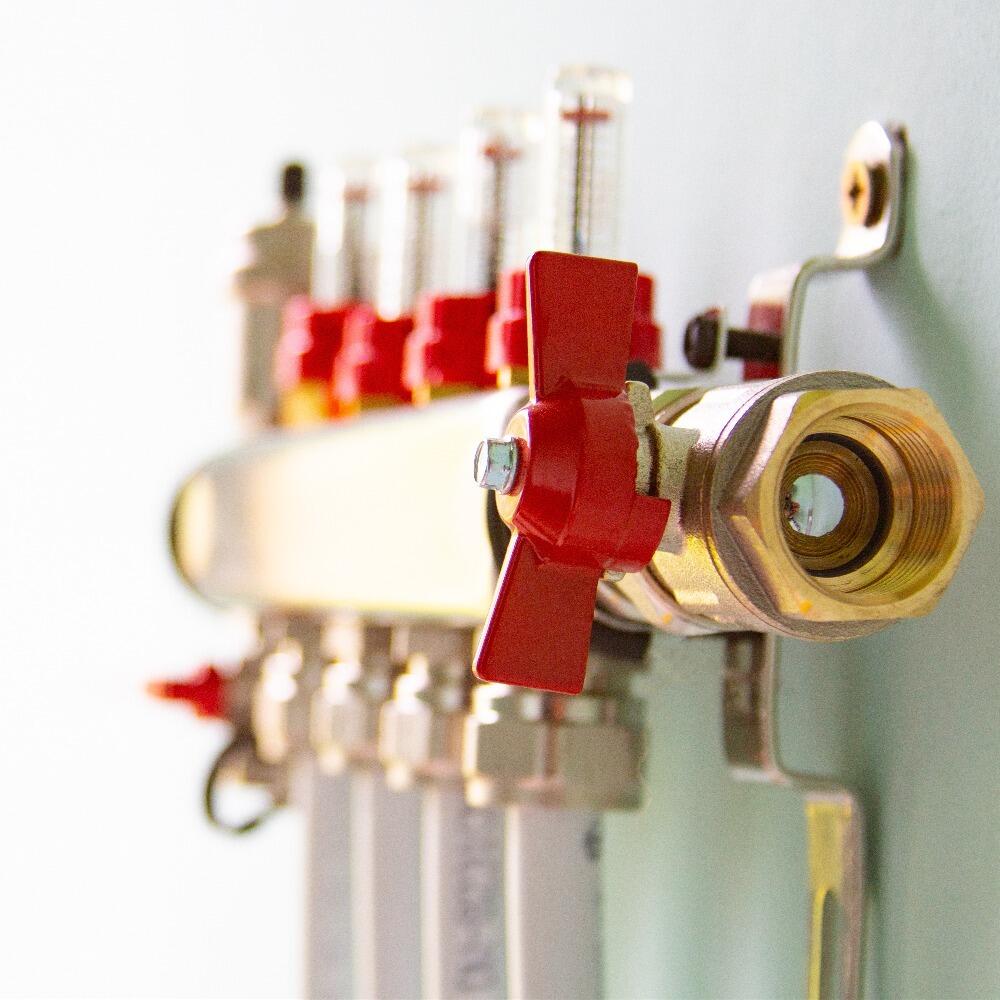
Ball valves are available in various materials, including brass, stainless steel, PVC, and various copper alloys. Copper alloy ball valves are particularly important in plumbing and HVAC systems due to their excellent thermal and corrosion resistance.
Copper alloy ball valves are made to BS EN 13547 standards, ensuring they meet stringent requirements for quality, performance, and safety.
Series A vs Series B Ball Valves
Series A Valves
Designed for flanged and threaded end connections.
Suitable for higher pressure/temperature ratings, aligning with those specified in the flange standards, EN 1092-3.
Series B Valves
Designed for flanged, threaded, capillary, compression, and loose nut/union end connections.
Have lower allowable pressures at elevated temperatures compared to Series A valves, making them suitable for applications with less demanding pressure/temperature requirements.
Methods of Operation
Ball valves can also vary by how they are operated, i.e. opened or closed:
Lever, Tee or Butterly Handle: These are designed to be operated so a 90° turn in the handle turns the flow on or off. When the handle is parallel to the flow passage, the valve is in the open position.
Handwheel: Offers manual operation, commonly used in larger or higher-torque applications.
Key: Used for valves with a shield around the stem, providing secure access and operation.
Gearbox or Actuator: Suitable for automated operation, allowing remote or mechanical control of the valve.
Full Bore vs Reduced Bore
Ball valves can be classified as full bore or reduced bore, depending on the size of the flow passage through the ball:
Full Bore Valves
The internal diameter of the valve is the same as the pipe diameter, allowing maximum flow with minimal pressure loss. Ideal for applications where maintaining flow rate and pressure is critical.Reduced Bore Valves
The internal diameter is smaller than the pipe diameter, slightly restricting flow and creating some pressure drop. Suitable for applications where exact flow rate is less critical, offering a cost-effective solution due to reduced material usage.
Ball Valve Size Classification
When choosing ball valves, selecting the correct size is essential to ensure compatibility with your piping and overall system requirements. The table below outlines common ball valve sizes along with their corresponding dimensions for various end types, including threaded ends, capillary ends, and compression ends suitable for copper and plastic tubes. This guide will help you identify the right valve size for your application, ensuring a proper fit and optimal system performance.
Nominal Valve Sizes | ||||
---|---|---|---|---|
DN | Threaded Ends | Capillary ends | Compression ends for | |
Copper Tube | Plastic Tube | |||
DN 10 | 3/8 | 10 | 10 | 12 |
DN 15 | 1/2 | 15 | 15 | 16 |
DN 20 | 3/4 | 22 | 22 | 20 |
DN 25 | 1 | 28 | 28 | 25 |
DN 32 | 1 1/4 | 35 | 35 | 32 |
DN 40 | 1 1/2 | 42 | 42 | 40 |
DN 50 | 2 | 54 | 54 | 50 |
DN 65 | 2 1/2 | 66.7 | 66.7 | 63 |
DN 80 | 3 | 76.1, 88.9 | 76.1, 88.9 | 75 |
DN 100 | 4 | 108 | 108 | 110 |
Key Factors to Consider When Selecting a Ball Valve
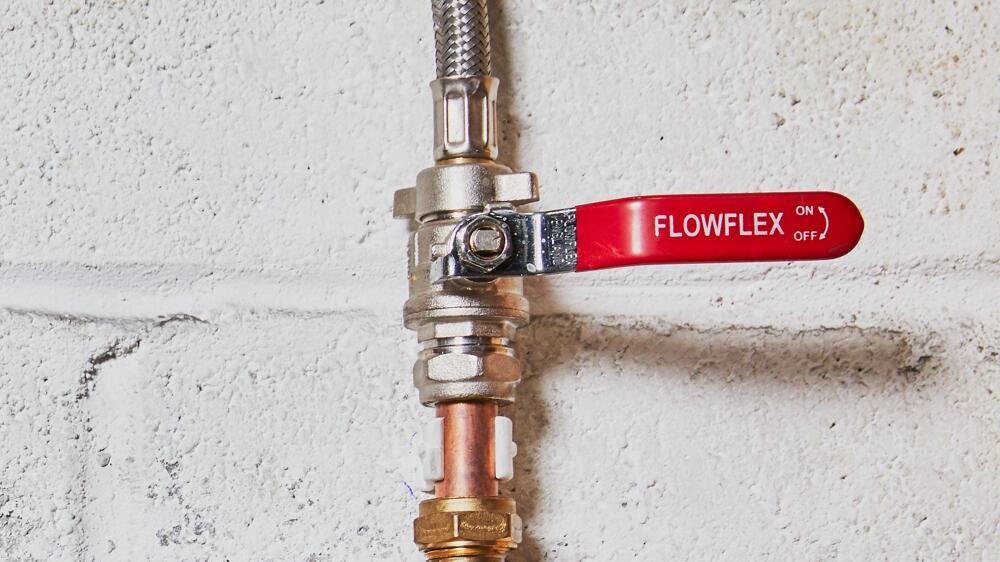
When selecting a ball valve, consider the following factors:
Material Compatibility: Ensure the material of the ball valve is suited for the liquid or gas it will carry, but also the tube it will connect to and the surrounding environmental conditions.
Pressure and Temperature Ratings: Check that the valve can handle the design system pressures and temperatures, especially when choosing between Series A and Series B valves.
End Connections: Choose the correct connection type (e.g., flanged, threaded, capillary, or compression) based on required working conditions, the safety considerations for your site and the skill level of your labour to ensure a secure and leak-free installation.
Operation Mechanism: Decide between manual or automated (actuated) operation based on design requirements, especially in industrial or hard-to-access installations.
Compliance with Standards: Verify that your ball valves are compliant with their relevant standards to ensure safety and high-quality performance in your applications.
Advantages and Disadvantages of Ball Valves
Ball valves are popular due to their ease of use, reliability, and versatility, but they also come with some limitations. This section highlights the key advantages and disadvantages of ball valves to help you make an informed choice for your applications.
Advantages
Quick and Easy Operation: Ball valves require only a 90-degree turn to open or close, allowing for fast and straightforward operation.
Excellent Sealing Capabilities: The tight seal provided by the ball ensures minimal leakage, making them highly reliable in critical applications.
Minimal Pressure Drop: Full bore ball valves allow for unimpeded flow, reducing pressure loss and maintaining system efficiency.
Durability and Longevity: Ball valves are designed to withstand high pressures, temperatures, and corrosive environments, offering a long service life with minimal maintenance.
Versatility: Available in various sizes, materials, and configurations, ball valves can be tailored to suit a wide range of applications, from domestic plumbing to industrial systems.
Limitations
Not Suitable for Throttling: Ball valves are not recommended for throttling applications as partial opening can cause wear and damage to the ball and seats.
Limited Flow Control Precision: Compared to other valve types, ball valves offer less precise control over flow rates.
Potential for Cavitation and Wear: High-velocity flow through a partially open ball valve can lead to cavitation, which may cause wear and erosion over time.
Size and Space Considerations: Ball valves, especially those with actuators, can be bulkier than other types of valves, requiring more installation space.
Performance of Flowflex Ball Valves
Flowflex Ball Valves are designed and manufactured to meet rigorous quality standards, including compliance with BS EN 13547. This ensures they offer reliable performance and durability across various applications. Below, we provide key performance data illustrating their effectiveness under different pressures and temperatures, highlighting their suitability for diverse applications:
All working conditions assume that the components have been assembled and connected correctly, and adhere to their respective tube compatibility.
If you are planning to use our products in applications outside the scope of our recommendations, approval must be sought from us beforehand. Please contact us in these cases.
611 & 711 Compression Ball Valves
Temperature (°C) | Pressure (Bar) |
---|---|
15mm to 28mm | |
30 | 16 |
65 | 13 |
95 | 10 |
> 28mm to 54mm | |
30 | 16 |
65 | 10 |
95 | 7 |
PX811 Union Ball Valve
Temperature (°C) | Pressure (Bar) |
---|---|
PX811 Range | |
-10 | 40 |
100 | 40 |
120 | 36 |
150 | 30 |
170 | 26 |
180 | 24 |
The performance of Flowflex Valves depends on proper installation and regular maintenance. For tips on how to care for your Flowflex Valves, explore our guidance here:
Read Now
Installation and Maintenance Tips for Flowflex Valves
Conclusion
Ball valves are essential components in various systems, providing reliable flow control with minimal maintenance. By understanding the differences in materials, bore types, operating elements, and end connections, you can select the right valve for your specific needs.
Flowflex copper alloy ball valves are made to BS EN 13547, offering enhanced safety, performance, and compliance, making them an excellent choice for plumbing and heating applications. Choosing the correct ball valve ensures efficiency, longevity, and peace of mind in your installations.
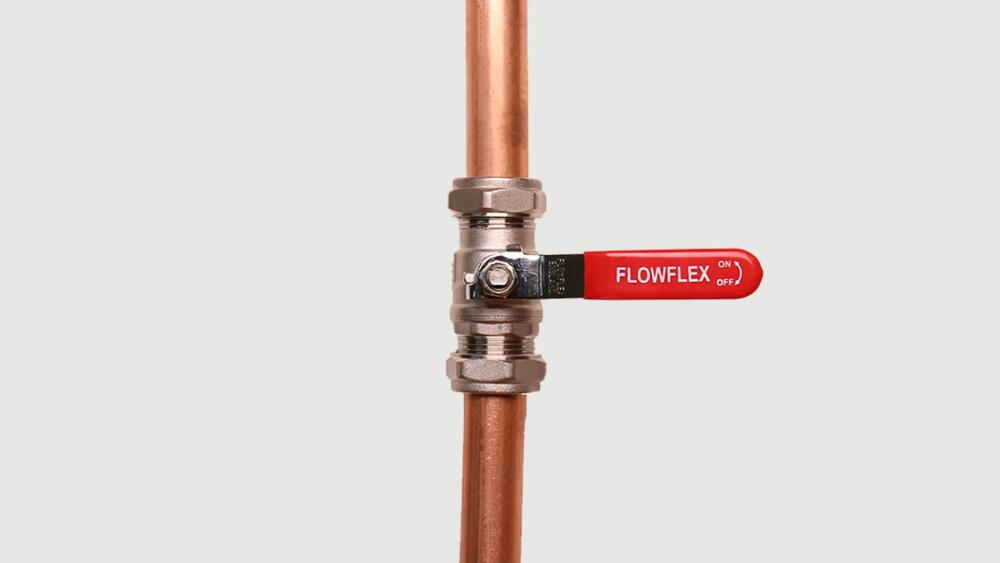
Ball Valves
Related Articles
-
-
-
-
-
Sep 9, 2024
Any Questions?
Our team is available for you anytime.