Support
Technical Information
Gate Valves Product Range
General Specification
This general specification provides an overview of the key features and capabilities of the product range. However, it is important to review the specific technical details and credentials of each individual product before use, as these may vary. Always verify that the product meets your specific requirements and standards for your intended application.
Products
This technical data sheet outlines the general specifications for the products listed below. Please be aware that specific details may vary between products. For precise information tailored to each product, please consult the relevant product page on our website.
Product Codes
L196, L197, L198, L198LS, P474, P474LS
Approvals
Flowflex holds ISO certifications independently audited by the British Standards Institute, ensuring credibility and trust with consumers, clients, and business partners alike. We take pride in these certifications and are committed to continuous improvement to better serve our clients.
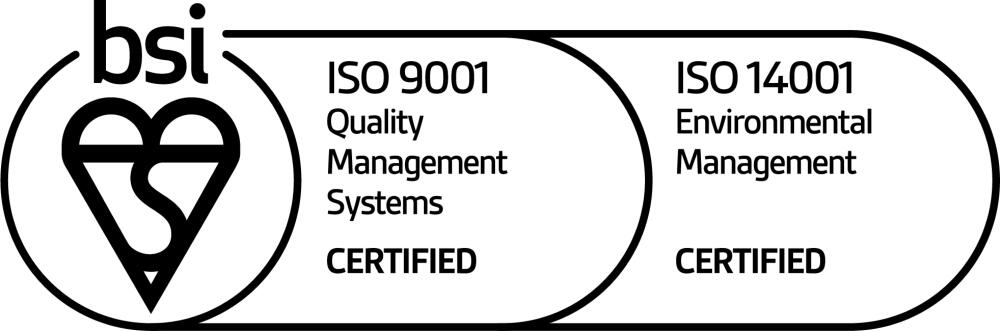
Standards
The products in this range are manufactured in accordance with the following standards to ensure superior quality, safety, performance, and compatibility:
Manufacturing
The products in this range are manufactured in accordance with the following standards:
- BS EN 12288: Gate Valves
Connections
The products in this range are engineered to establish connections in compliance with the following standards:
- BS EN 1254-2: Products With Compression Connections
- ISO 228-1: Parallel Threads
Complimentary Products
The products in this range are specifically designed to work with products that adhere to the following standards:
- BS EN 1057: Copper Tube for Water and Gas in Sanitary and Heating Applications
- ISO 228-1: Parallel Threads
Working Conditions
All working conditions assume that the components have been assembled and connected correctly, and adhere to their respective tube compatibility.
If you are planning to use our products in applications outside the scope of our recommendations, approval must be sought from us beforehand. Please contact us in these cases.
Gate Valves
Applicable Products
L196, L197, L198, L198LS, P474, P474LS
Temperature (°C) | Pressure (bar) |
---|---|
PN20 | |
-10 | 20 |
100 | 20 |
120 | 17.2 |
150 | 13.0 |
170 | 10.3 |
180 | 9.0 |
PN16 | |
-10 | 16 |
100 | 16 |
120 | 13.5 |
150 | 9.5 |
170 | 7.0 |
Applications
Products in this range are designed and manufactured to deliver reliable performance in the following applications. However, please review each product individually for detailed information on its specific intended uses.
- Hot and Cold Water Services to EN 806
- Closed Heating Systems to EN 12828
- Drainage Systems
- Fire Protection Services to EN 12845
- Chilled Water Systems
- Irrigation
If you plan to use our products outside of the specified applications, you are required to obtain our approval before proceeding with installation.
Assembly
How To Prepare Your Copper Pipe
Equipment
Tools
- Pipe Cutter
- Deburring Tool
- Hand Protection
Supplies
- Copper Pipe
Installation Steps
Cut Your Pipe To Size
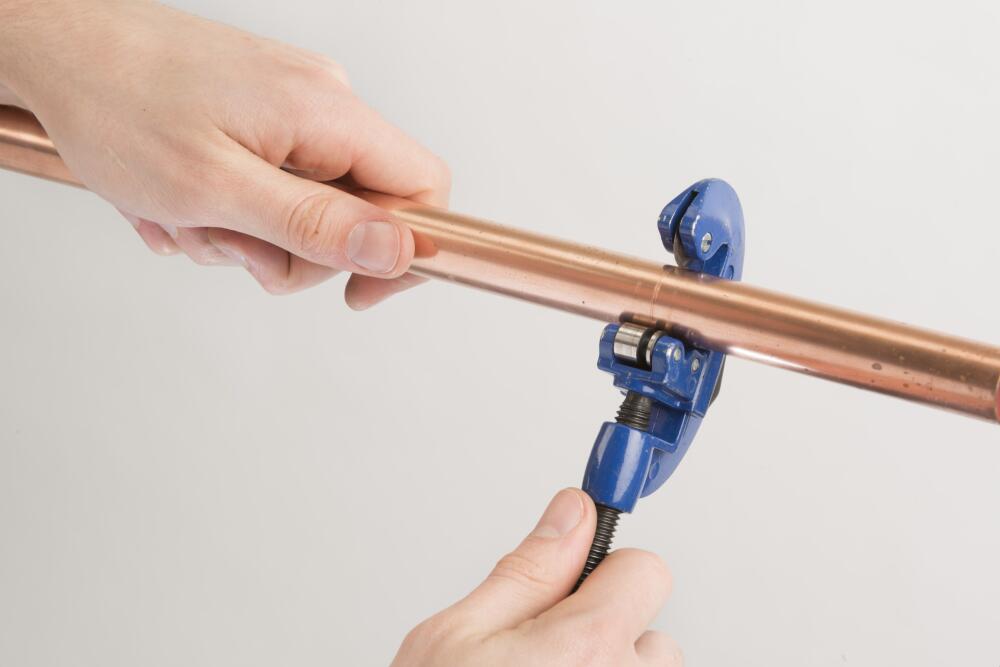
Cut your pipe cleanly across the tube diameter using a good quality pipe cutter or rotary pipe cutter.
Cut Your Pipe Accurately
It is important to ensure that the pipe ends are clean and cut square. Failure to do so could impact on the quality of your jointing. If your cut is not flat, or your pipe is too short, the pipe may not hit the pipe stop compromising the joint integrity. Too long and you may introduce strain into the whole system.
Clean The Socket Of The Pipe
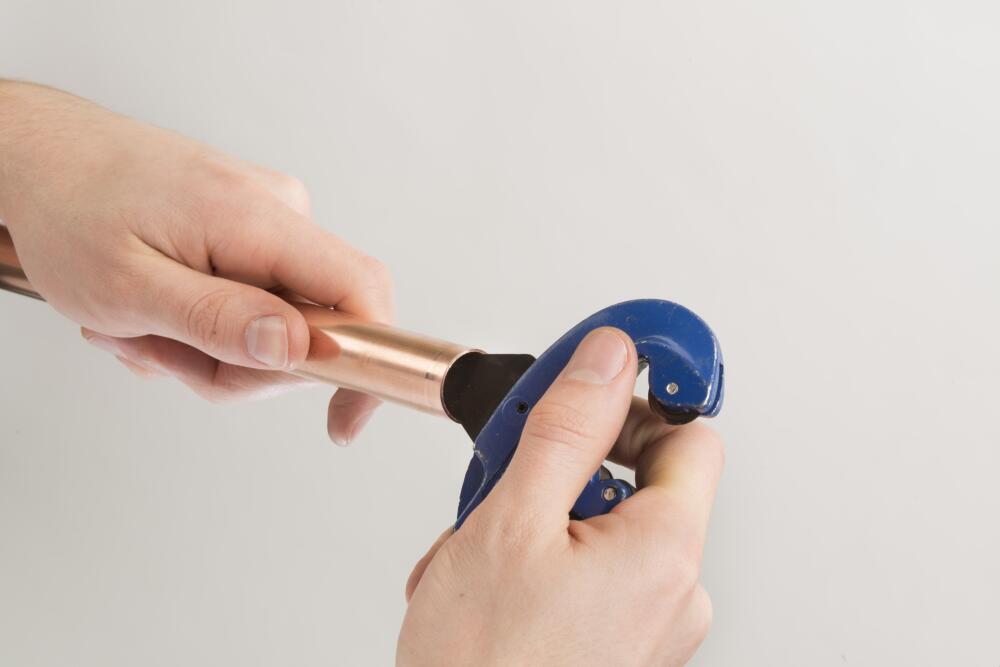
Using your deburring tool, make sure the inside of the pipe is smooth and will not interfere with the flow.
Clean The Outside Of The Pipe
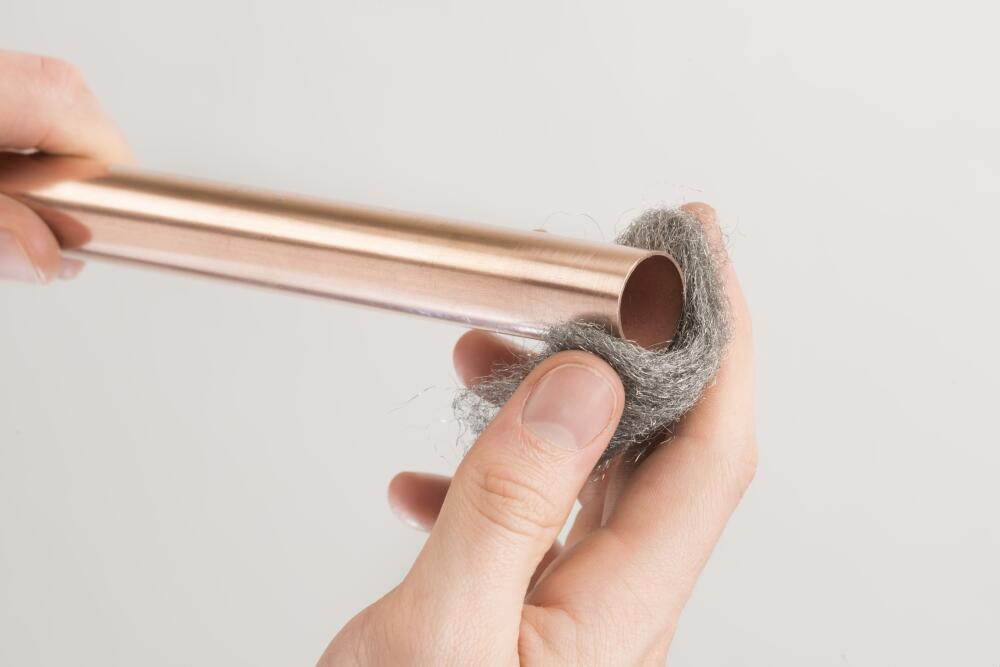
Clean the outside of the pipe, making sure that there is no pipe residue, dirt or grit is present near the joint. Failure to remove all oxides and any material where the fittings and tube overlap can interfere with the capillary action and thus will reduce the strength of the soldered joint, resulting in failure.
To the same effect, over zealous cleaning can result in too much material being removed, resulting in a loose fit and failure.
How To Install Large Flowflex Compression Fittings
Equipment
Tools
- Adjustable Spanners
Supplies
- Copper Pipe
- Large Compression Fitting
Installation Steps
Connecting
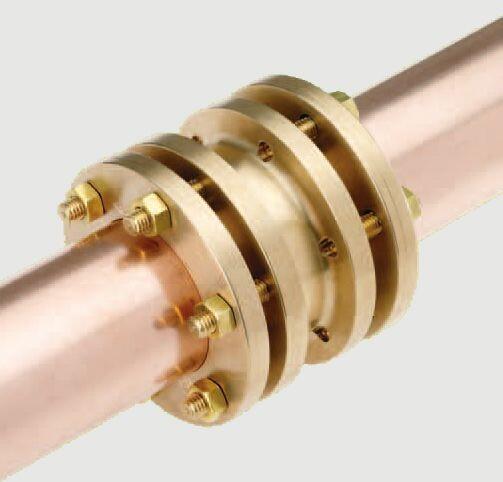
Place the flange and compression ring on to the tube. Insert the tube firmly into the fittings body, ensuring that the compression ring seats centrally and that the tube makes firm contact with the tube in the body.
The compression flange should be parallel to the face of the body to indicate that a sound joint has been made.
Do Not Overtighten The Nuts
Tighten the Nuts
Bring up the compression flange, and tighten the nuts by hand. Using a spanner continue to tighten the nuts diagonally in increments on ½ turn, to a minimum of 2 turns and maximum of 2 ½ turns.
Check For Leaks To Be Sealed
If after assembling the joint in accordance with the instructions above a slight weep is experienced – as occasionally may happen – it will readily be corrected by the application of a smear of an approved sealing compound to the sealing faces.
How To Assemble Compression Connections On Copper Pipe
Equipment
Tools
- Adjustable Spanners
Supplies
- Compression Fittings
- Copper Pipe
Installation Steps
Assembly The Fitting Around The Tube
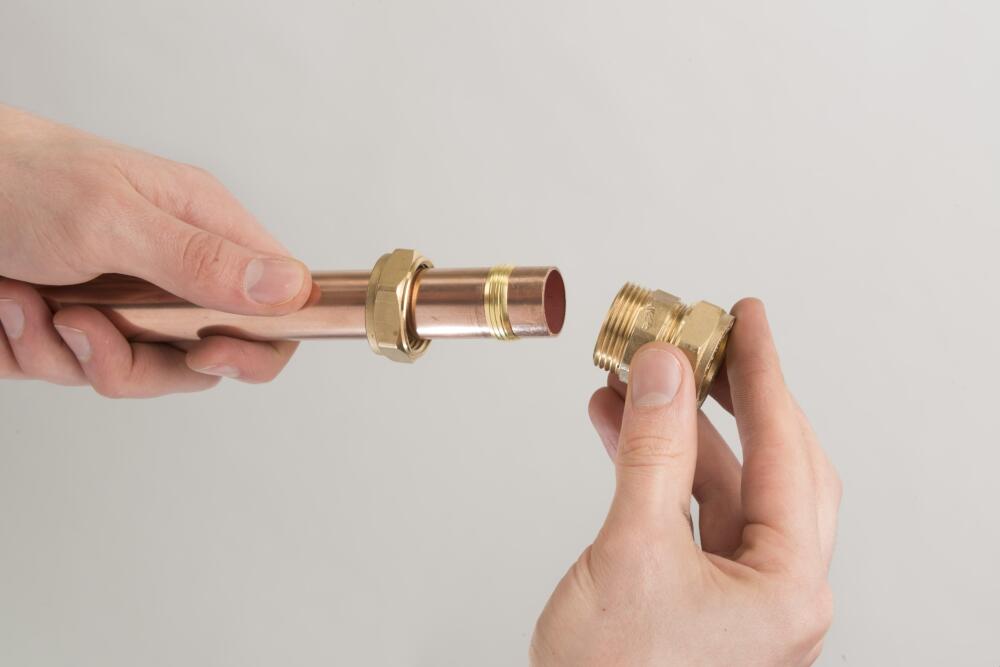
Remove the compression nut and compression olive, then put the nut on the tube, followed by the olive. Insert the tube end up to the fitting's tube stop. Slide the olive and the nut down to the fitting body. Tighten the nut using your fingers to secure the fitting in place.
Only Use Flowflex Olives with Flowflex Compression Fittings
Warranty only valid when compression fittings are used with Flowflex olives supplied with the fitting.
Tighten The Nuts
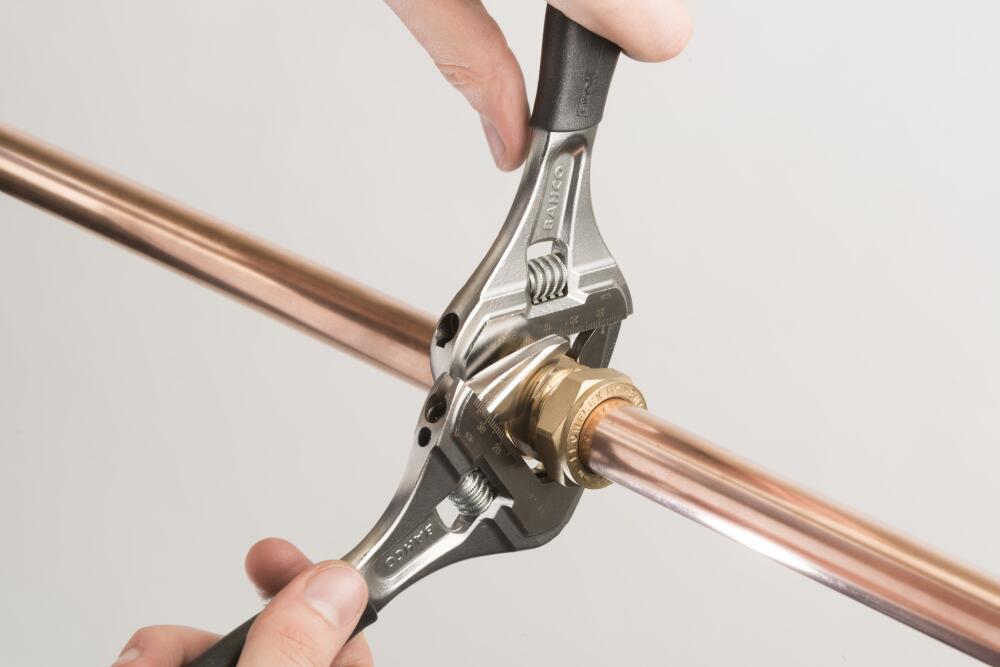
Tighten the nut further using open ended or adjustable spanners, using the spanner flats incorporated into the fitting body and nut. The second spanner must be used to prevent the fitting rotating as the nut is tightened.
A few drops of light oil can be used on the threads to assist the turning. This can be especially helpful on sizes 35mm and above. When jointing stainless steel or annealed (R220) copper tube some variation may be needed – the nut may be tightened further if necessary.
Do not overtighten the nuts
Over-tightening can be detrimental to both the nut and the olive, weakening the joint and causing issues later when servicing. Please see below for more information on guidance on how to tighten your Flowflex Compression Fittings.
Size | Turns |
---|---|
< 28mm | 1 1/4 Turns |
>= 28mm | 3/4 Turns |
Torque Settings
Size | Torque |
---|---|
15mm | 30 - 35 Nm |
22mm | 45 - 50 Nm |
28mm | 55 - 60 Nm |
35mm | 105 - 110 Nm |
42mm | 150 - 155 Nm |
54mm | 240 - 245 Nm |
Commissioning
Testing Your Installation
Flowflex products are designed to comply with normal installation specifications, such as BS 806-4. As such, we strongly recommend that all systems are thoroughly tested upon completion. Whenever possible, completed systems should also be flushed to remove any debris, ensuring optimal performance and longevity.
Testing Hydraulic Installations
For hydraulic-based installations, the system should be tested to 1.65 times the system’s maximum operating pressure. This pressure should be maintained for at least 30 minutes to help identify any potential issues and confirms the system’s integrity.
If higher test pressures are required for your specific application, please contact us for further guidance and support.
Read Now
Testing Plumbing Installations
Considerations
Stress Corrosion Cracking
Stress Corrosion Cracking (SCC) occasionally occurs in metals when they are exposed to both a corrosive medium and tensile stresses. For brass used in compression fittings, SCC is almost always introduced during installation due to over-tightening and contamination by a stress-cracking agent.
What Causes Stress Corrosion Cracking
SCC occurs when the following conditions are met simultaneously:
A Susceptible Material: In this context, brass.
Contaminated Environment: In this case moisture, ammonia or ammoniacal compounds,
Tensile stress: Application of tensile stress on the material.
SCC In Brass Compression Fittings
The most common cause of SCC in brass compression fittings is exposure to ammonia or ammoniacal compounds. These substances are found in various sources, including cleaning fluids, refrigeration gases, sewage waste products, building materials, insulating materials (especially foams), and flame and smoke retardant treatments.
Moisture plays a significant role in the SCC process. It acts as a catalyst by allowing corrosive substances to accumulate and become more concentrated. This is particularly problematic in chilled water installations, where insulating materials can retain condensed moisture and keep it in close contact with the surface.
How Can I avoid Stress Corrosion Cracking
Avoiding SCC is straightforward when following good installation practices and the manufacturer’s instructions. Alternatively, consider using fittings made of copper or bronze for your application.
For Flowflex Brass Compression Fittings, alongside our installation instructions, the following advice is crucial:
Proper Thread Tightening: When tightening male taper threads into female parallel threads, do not over tighten. Use PTFE tape or an approved sealant to ensure a secure fit.
Use the Correct Tools: Use a flat-faced, high-quality spanner that matches the size of the nut.
Lubrication for Larger Fittings: For compression fittings larger than 28mm, apply light oil to the threads. This reduces the force needed to tighten the fitting and decreases stress.
Avoid Stress-Cracking Agents: Ensure no stress-cracking agents are present near the installation. If uncertain, consider using a different jointing method, such as Flowflex Copper Capillary fittings or Flowflex Copper Press.
Protection in Aggressive Environments: In environments conducive to SCC, you should protect Flowflex Brass Compression Fittings from aggressive moisture by wrapping the fittings with an appropriate impervious tape.
Overall, installers should ensure that all Brass Compression connections are not over tightened, and that the environment into which they are installed is not conducive to the cause of Stress Corrosion Cracking as outlined above.
Electrical Continuity
Equipotential Bonding forms an important part of an installation, which ensures that all metalwork may be earthed or at least has the same potential to reduce the risk of equipment damage and personal injury. Isolated fittings or valves are not required to be bonded.
Flowflex Compression Fittings provide guaranteed electrical continuity when correctly assembled with BS EN 1057 Copper Tube.
After all plumbing work has been completed, always ensure continuity checks are conducted by a qualified electrician in accordance with regulations (BS 7671).
Read Now
Electrical Continuity in Plumbing
Any Questions?
Our team is available for you anytime.